
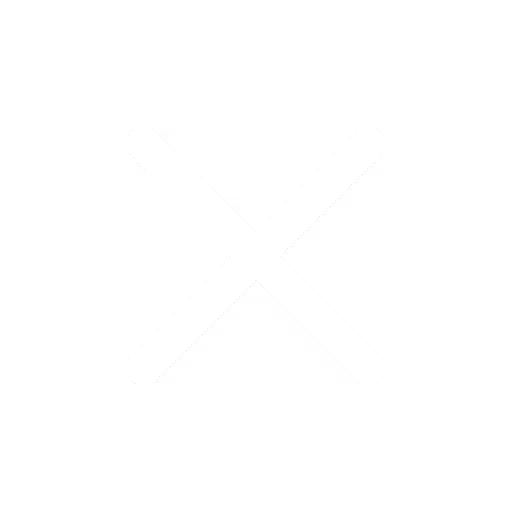
Vapor Recovery

Methane Leak Detection

Production Optimization

Integrated Capabilities

Sustainability

About

Careers

Contact Us

Methane Leak Detection

Product Optimization

Integrated Capabilities

Sustainability

Knowledge Center

Within the oil and gas industry, capturing, processing, and reusing hydrocarbons that would otherwise be lost as vapors is quickly becoming an essential practice and is only becoming more paramount with every passing day. To stay ahead of the curve operators can deploy Vapor Recovery Units (VRUs) to help maximize efficiency, reduce environmental impact, and increase profitability. Whether you're managing oil and gas production, transportation, or storage, understanding how VRUs work and the various types and applications is crucial to optimizing your operations.
Here we will cover everything you need to know about VRUs, including how they operate, the different types you’ll encounter in the industry, and why these systems are indispensable for modern oil and gas operations. By the end, regardless of your experience level in the industry, you’ll have a solid grasp of how the vapor recovery process works.
Let’s start with the regulatory side of things. If you’re in the oil and gas industry, you know that emissions regulations are tightening and they can feel suffocating to a company. Governments around the world are mandating lower emissions, and failing to comply with these standards can lead to hefty fines, operational restrictions, and damaged reputations. Vapor recovery systems offer a solution to this problem by capturing harmful gases like volatile organic compounds (VOCs) and methane, which would otherwise escape into the atmosphere.
Without vapor recovery, companies run the risk of falling out of compliance with local, state, or even international regulations. And it’s not just about avoiding fines; having a reliable vapor recovery system in place shows that your company is committed to environmental responsibility, something that can strengthen your relationships with customers, regulators, and the public. In a world where corporate social responsibility is more important than ever, vapor recovery is a step toward being a more sustainable, forward-thinking business.
Beyond just the regulations aspect, there lies the underlying implications of environmental impact. When oil and gas companies release VOCs and methane into the atmosphere, it does not just harm the atmosphere and the air we breathe—it contributes significantly to climate change. Methane is a potent greenhouse gas that traps heat in the atmosphere much more effectively than carbon dioxide. If we, as a society, are serious about tackling climate change, then capturing methane emissions in energy production is critical.
Vapor recovery systems help oil and gas companies drastically reduce their carbon footprint by capturing these harmful gases and preventing them from escaping into the environment. That’s not only good for the planet but also for the people living near oil and gas operations. Cleaner air, fewer emissions, and reduced pollution all contribute to a better quality of life for local communities. When companies invest in vapor recovery, they are investing in a cleaner, safer future for everyone.
While we have talked a lot about emissions, vapor recovery is a vital source for increasing revenue for oil and gas producers. The gases that are captured by vapor recovery systems, like methane and propane, are not just waste; they’re valuable resources. By capturing and repurposing these gases, companies can create additional revenue streams. Taking emissions practices from a cost center to a profit center. Whether the recovered gases are reused in production or sold, vapor recovery turns what would have been lost into something profitable.
And it’s not just about selling gases. Vapor recovery also improves operational efficiency by reducing waste and preventing product loss. Every bit of vapor that escapes into the atmosphere represents a loss of valuable product. By capturing those vapors, companies are essentially putting a stop to that loss. In a business where efficiency is key to profitability, vapor recovery systems make a significant difference.
Learn more about why vapor recovery is important.
Vapor recovery units (VRUs) are essential in the oil and gas industry for reducing emissions and enhancing efficiency. But what goes into designing these systems?
A VRU captures vapors that would otherwise be released into the atmosphere, and injects it into the midstream gathering system. Engineering plays a vital role in ensuring this process is efficient, safe, and compliant with regulations.
The "muscle" of the system, pushing vapors through while minimizing energy waste and leaks.
The inlet scrubber captures entrained liquids and automatically discharges them to the tanks. The discharge separator serves as the compressor oil reservoir.
Modern VRUs feature advanced automation to monitor and adjust key parameters for safe and efficient operation.
Design Considerations: Flow rates, environmental regulations, safety, and durability are critical in VRU design. Engineers must balance efficiency, compliance, and long-term performance to keep systems running smoothly in harsh conditions.
Learn more about the engineering designs of vapor recovery
A VRU is a device that captures hydrocarbon vapors, compresses them, and turns the product into a usable resource rather than letting it escape into the atmosphere to do harm to our environment. In doing so, VRUs not only help reduce emissions but also recover valuable vapors that can be reused or sold, offering a dual benefit of environmental protection and increased revenue. Now, who doesn't love that? So, let's take a detailed look at how VRUs work, breaking down the process step by step.
Learn more about the operations of vapor recovery
During the oil and gas production and storage process, hydrocarbon vapors can be released. These vapors accumulate as produced oil experiences pressure and temperature fluctuations. A VRU system is designed to capture these vapors before they escape through venting or flaring.
When the sensors in a VRU detect that the vapor pressure has reached a certain level, the system automatically opens valves that direct the vapor through a series of pipes into the VRU’s compressor. This happens seamlessly and continuously, without the need for human intervention. The goal of this initial step is simple: capture as much vapor as possible before it can be lost to the environment.
The success of total vapor capture is largely reliant on sophisticated automation. By continuously monitoring vapor levels and collecting the flash vapors as necessary, the VRU ensures that operations proceed efficiently with minimal downtime or manual involvement.
Once the vapor is captured, it is compressed to reduce its volume with sufficient pressure to inject it into the pipeline infrastructure. This compression serves two main purposes:
In some cases, the vapor may undergo multiple stages of compression depending on the initial vapor pressure and the specific needs of the operation. Multi-stage compression is especially important in high-pressure applications where controlling the vapor flash from multiple sources is critical.
After the compression stage, the vapor moves into the cooling phase. This is where the separation of the vapors potentially happens. When cooled, hydrocarbons with different boiling points begin to condense. Heavier hydrocarbons like propane and butane condense first and turn into liquid, which can then be separated from the gas stream via a knockout tank before the remaining gas enters the sales line to be sold.
In a VRU, cooling is typically done using a heat exchanger that brings the temperature of the compressed gas down to the required level for custody transfer. Depending on the setup, ambient air run through the cooler by a fan is typically used to cool the vapors, causing the heavier components to condense into liquid form. This liquid is collected in a separator and sent off for further processing or sale.
This cooling and condensation step is critical for separating valuable liquids from gases, allowing companies to make the most out of their captured vapors.
After being cooled, the heavier hydrocarbons have condensed, and the next step is separating the liquid from the gas. The separated liquids—such as propane and butane—are stored and can be sold as fuel or used in other processes. The remaining gases, primarily methane, is injected into the gathering system.
The separation process occurs in a phase separator, which is specifically designed to divide the gas from the liquids efficiently. The liquids are collected for storage, sale, or further processing, while the gas is typically routed for additional use, such as being sold as natural gas or utilized onsite for energy generation.
By ensuring both liquid and gas hydrocarbons are captured and separated, VRUs maximize the amount of usable material recovered, preventing waste and boosting efficiency for the oil and gas producer.
The final step in the vapor recovery process is to deal with the recovered gas, typically methane. Methane is an extremely valuable resource that can be used in several ways, including:
By the end of the process, a VRU has effectively captured, compressed, cooled, and separated both liquid and gas hydrocarbons, turning what could have been waste into valuable resources that contribute to the operation’s profitability and helped minimize emissions.
Not all VRUs are the same. In fact, the specific needs of an operation will ultimately dictate the type of VRU you should use. Whether you’re dealing with low-pressure vapor streams in marginal wells or having to mitigate high-volume emissions, there’s a vapor recovery solution available to you. Let's look at the main applications of vapor recovery.
Conventional VRUs are very versatile pieces of equipment, capable of handling a wide range of vapor pressures and volumes. These units are typically found in operations where crude oil or natural gas is stored, making them a common choice for a variety of applications.
In a conventional VRU:
Conventional VRUs are a reliable option for many oil and gas facilities since they can handle both moderate and high vapor pressures, making them an efficient and valuable choice for various production and storage needs.
Low-pressure VRUs are designed with the small operator in mind, where vapor pressures are lower, such as marginal wells or gas-gathering systems. These smaller units are perfect for smaller production sites or remote locations where vapor volumes are lower but regulatory compliance and efficiency are greatly needed.
Key features of low-pressure VRUs include:
Essentially, low-pressure VRUs ensure that even small-scale operations can capture and recover valuable hydrocarbons without excessive energy consumption or cost and help to align producers with continued regulation compliance.
For larger well operations with typically high vapor pressures, such as gas processing plants, high-pressure VRUs are the go-to solution. These units are designed to handle large vapor volumes and high-pressure situations safely and efficiently in many different conditions.
In a high-pressure VRU:
High-pressure VRUs are essential for operations with significant vapor emissions. They prevent the loss of hydrocarbons and ensure that even the largest vapor volumes are captured and processed.
If you are familiar with the oil and gas industry then you may already know that excess gases are often flared, or burned off, into the atmosphere to reduce pressure or manage safety concerns. While flaring is a common practice in the oil and gas industry, it does release harmful emissions. Flare gas VRUs are designed to capture these gases and turn them into usable resources.
Here's why using a VRU instead of flaring is important:
VRUs that are used as an alternative to flaring are critical pieces of equipment that reduce greenhouse gas emissions and improve the overall sustainability of oil and gas operations, all while helping you stay compliant and produce more resources.
Portable VRUs offer flexibility for operations that need temporary or mobile vapor recovery solutions. These units can be relocated to different sites quickly, making them ideal for projects that require temporary setups or are in remote areas where a permanent VRU installation isn’t feasible.
Portable VRUs are:
For maintenance work, short-term projects, or temporary facility expansions, portable VRUs provide a cost-effective and efficient vapor recovery solution.
Learn more about the applications of vapor recovery
At Flogistix, we’re more than just a vapor recovery unit company— we’re your partner in optimizing your operations for maximum efficiency and profitability. We specialize in creating custom vapor recovery solutions tailored to the unique needs of your site, whether you’re managing crude oil storage, natural gas processing, or pipelines.
With Flogistix you get:
Ready to take the next step in optimizing your vapor recovery process? Contact us today to see how we can help you transform your operations.
Contact UsGot questions? Discover why VRUs matter and how they can help your operations in the FAQs.
The Importance of Vapor Recovery
Vapor Recovery Units Effectiveness
Is a Vapor Recovery Unit (VRU) Just a Compressor?
Overcoming Challenges in VRU Implementation
Regulation Benefits of Vapor Recovery
Revenue Benefits of Vapor Recovery
The Emissions Benefits of VRUs
How Does a Vapor Recovery Unit Work?